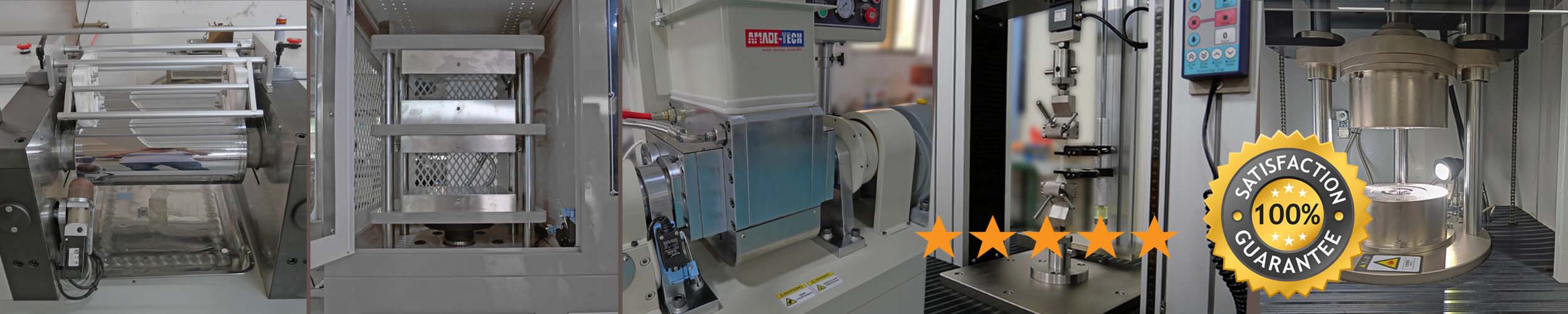
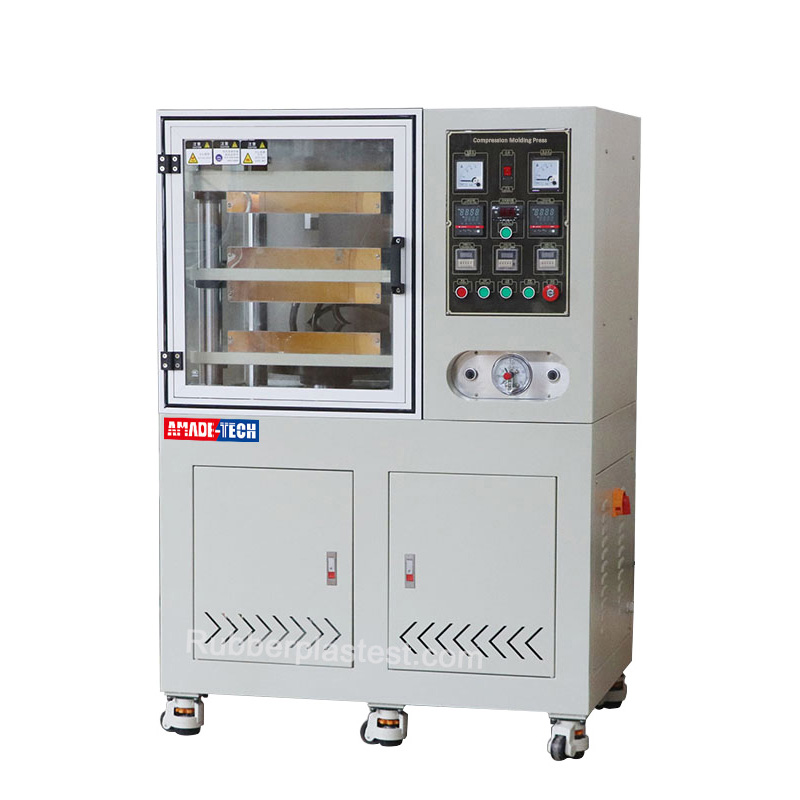
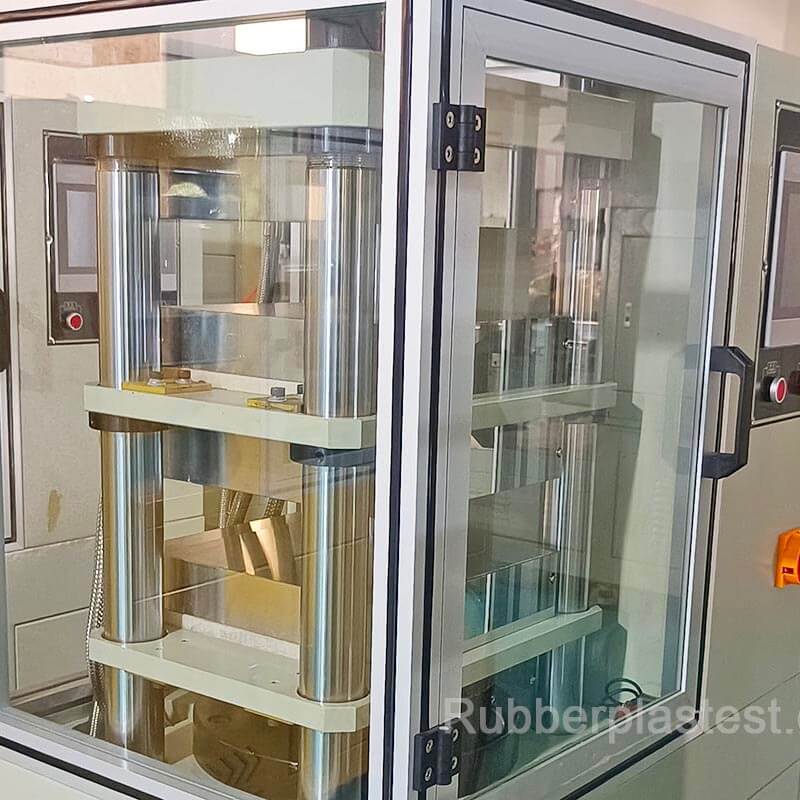
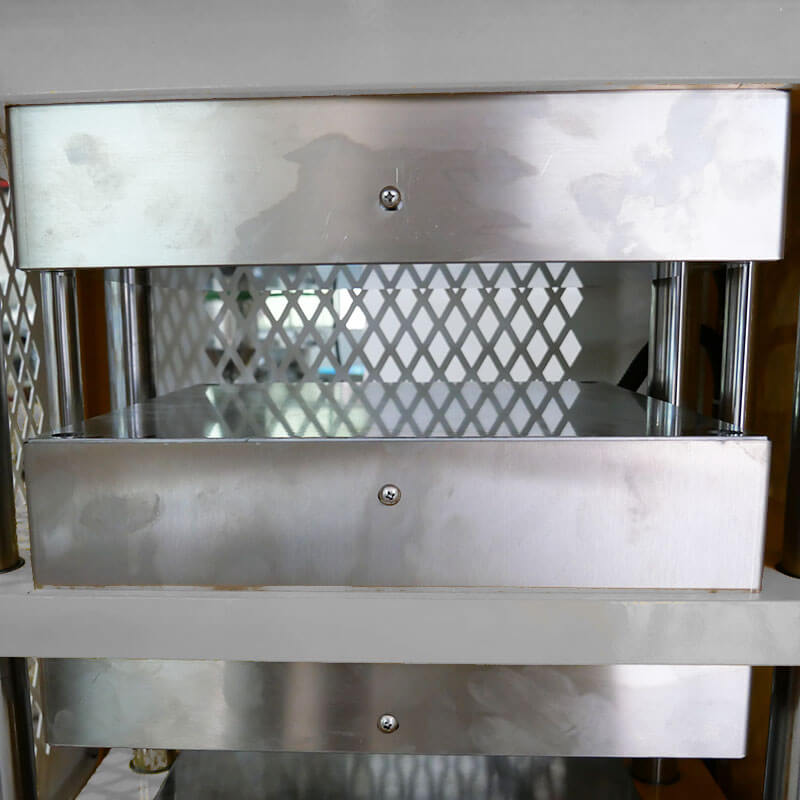
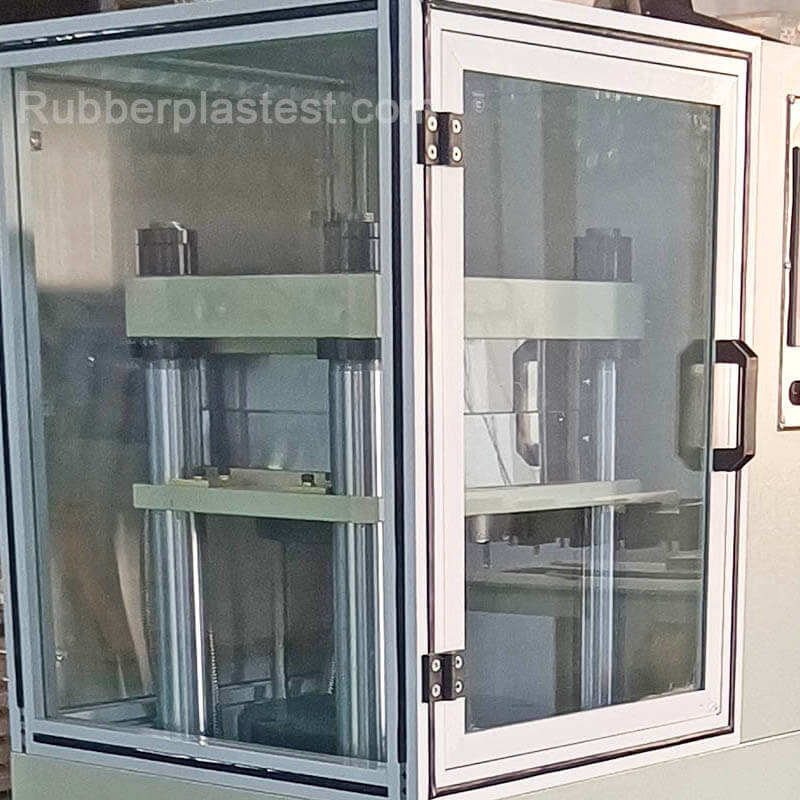
Lab Hydraulic Press
Model
AT-R7026 series
Applications
Lab hydraulic compress press for curing rubber test slabs or molding various sheet plastic samples for subsequent testing and comparison.
Lab Hydraulic Press Description
Lab Hydraulic Press is also called a plate vulcanizer or compression press. It owns at least two platens can be heated to a prescribed high temperature used to mold the mixed rubber compound at a specified pressure for a given period of time for achieving the purpose of vulcanization. In addition, it can also be used to hot press or mold PP, PA, PE, ABS and other resins or mixtures for conducting color comparison, formula testing and related mechanical tests.
The lab vulcanizing machine is mainly composed of hydraulic system, guide pillars, lifting platform, pressure platens and control system.
pressure plate structure
Hydraulic system
Our lab hydraulic press adopts floor-standing structure, which is mainly divided into upper and lower parts. The hydraulic system, which accounts for the heaviest weight, is located at the lower part of the machine, which plays a role in stabilizing the center of gravity at the bottom. You are allowed to open the doors to enable the main body of the hydraulic system to be exposed, which is convenient for maintenance and repair. According to different load requirements, we can configure the machine with hydraulic systems of different capacities, including 30T, 50T, 100T or specified by you.
Guide pillars & Platforms
The left side of the upper part of the machine is the vulcanization area or heat-press area. It is mainly composed of four precision guide pillars, three iron plate platforms, four pressure platens, and a protective cover. You can see four shining steel columns stand vertically on the base. If these four points are connected, it will form a standard rectangle. Each column passes through three guide holes at the corners of the three platforms. The top platform is locked on the top of the four columns with nuts forming a stable frame as a whole with strong load capacity. The movable platform in the middle is limited downward and can only move upward guided by the pillars under the action of external force. The geometric center of the bottom surface of the lowest movable platform is connected to the ram of the hydraulic cylinder to guarantee that the pressure is transmitted from bottom to top during operation. Three platforms divide the entire area into two layers of space. Depending on your actual needs, the machine can also be configured with only one layer.
Pressure Platens
For AmadeTech’s regular models, four pressure platens made of KDB high carbon steel are attached to the three platforms mentioned above to form two processing areas, and the parallelism between each two platens is less than 0.02 mm. Different sizes of pressure platens are available from us. Each platen has been finely processed and has the characteristics of high temperature resistance, corrosion resistance, fast heat transfer, and not easy to deform. The two upper platens used for heating have built-in heating tubes that can heat up the platens to 300°C, and are equipped with high-precision temperature sensors to collect real-time temperatures. We adopt P.I.D self-tuning mode with automatic temperature compensation function to ensure temperature stability and uniformity. If you want to pursue a more uniform platen temperature with a deviation of less than 1°C, we can also configure an additional oil heating device instead of electric heating as heating source. The two lower platens used for cooling the material have built-in water channels and can be connected to external tap water, which is used to achieve the purpose of one-time cooling and molding of the material. If you don’t want the cooling function, we can remove the two cooling platens. In addition, we can integrate the heating and cooling functions into two platens in the same layer, so that you can directly perform the cooling step after heating without transferring materials.
Human-machine Interface
We laid out the human-machine interaction device on the right side of the upper part of the machine. There are two types of operation panels for users to choose from: push-button panel and PLC touch screen panel. The push-button panel is covered with various control buttons, thermostat, pressure gauge and pressure adjustment knob, ammeters, timer, etc. You need to manually press the corresponding buttons to set required parameters, and start heating, platen closing, timing, platen opening, cooling functions, etc. Some of our push-button models also support automatic operation mode. The touch screen panel is the interface based on a PLC supporting multi-stage pressurization. You are available to use your finger to click on the screen to freely set the platen temperatures, preload pressure and time, exhaust pressure, exhaust number, exhaust time, multiple boost pressures, corresponding cure times, etc. The system has a built-in calculation formula, allowing you to input the length and width of the compression area for precise pressure application. During the vulcanization operation, the machine is able to automatically complete all operations according to the set molding program and generate processing curves. Moreover, the platen temperature, pressure, platen dynamic running diagram, real-time status, etc can be displayed on the screen in real time for you to view.
Lab Hydraulic Press - Technical Specifications
Model | AT-R7026 series |
Load capacity | 30t / 50t / 100t or customized |
Pressure sensor | Japanese platinum resistance sensor |
Pressure gradient | Pre-pressurization and boosting |
Platen material | SKD mold steel |
Platen surface treatment | Mirror chrome plating |
Platen hardness | HRC60 |
Platen area | 300 x 300 mm or customized |
Parallelism | ≦±0.02mm/m |
Temperature range | Ambient temp.~ 300℃ |
Temperature accuracy | ≦2℃ |
Heating mode | Electrical heating |
Cooling mode | Water circulation |
Working areas | Upper layer for heating and the lower layer for cooling / Or both are integrated into one layer |
Control mode | Manual / Auto |
Controller | Microprocessor + buttons / PLC+touch screen |
Dimensions | 920 mm (W) x 500 mm (D) x 1450 mm (H) |
Power supply | Three-phase, AC 380 V |
Weight | Appr. 700 kg |
Hydraulic Press Working Principle
The upper and lower pressure platens are heated to the required curing temperature and maintained at a constant temperature. The mold containing the rubber compounds is placed in the center of the lower pressure platen. The hydraulic system supplies pressure oil into the hydraulic cylinder under control to drive the piston to move upward to push the lower pressure platen upward until it touches the upper pressure platen and compresses the mold to ensure that the rubber material obtains the pressure required for vulcanization. After a certain period of time, the vulcanization is completed, and the pressure will be automatically relieved. Due to the dead weight of the piston and lower platen, the mold will automatically descend and exposed for removal. If necessary, the mold needs to be cooled by means of cooling water circulating through the pressure platens following the cure process.
Lab Hydraulic Press Features
- Different hydraulic press capacities are available from AmadeTech.
- It adopts high-precision wear-resistant guide pillars to ensure smooth lifting and lowering under strong loads.
- Pressure platens are fabricated from SKD mold steel of Rockwell hardness 60 HRC, and the surface has been treated by carburizing, chromium plating, polishing and other processes.
- The size of the pressure platens can be customized.
- The pressure platens have heating and water cooling functions.
- Adopts high-precision temperature sensor and P.I.D self-adjusting temperature control.
- The hydraulic system has an automatic pressure compensation function.
- Physical-button panel or PLC touch screen control panel is available.
- All electrical and water pipes are connected with flexible pipe fittings to avoid hindering the lifting and lowering of the pressure platens.
- Supports presetting of pre-pressing time, pre-pressing pressure, exhaust number and time, boost pressure, vulcanization time, etc.
- The molding process can also be dynamically displayed on the screen and monitored in real time. The vulcanizing curve is available to be displayed.
- The processing area is equipped with protective cover to guarantee the safety of the operator.
- The protective door is equipped with a safety self-locking device, which can automatically cut off all operations when opened.
FAQs About the Lab Hydraulic Press
When the hydraulic system is working, the ram is pushed upward. It will first drive the lowermost cooling plate to move upward, and then drive the middle cooling plate and heating plate in turn until it finally contacts the uppermost heating plate. The plates gradually apply pressure until it reaches the target value and then maintains it constant for a defined period of time. During this process, the pressure is automatically increased and decreased to hold the pressure. If there is insufficient pressure, the system will automatically compensate for the pressure. Note that if the rubber vulcanization is controlled by PLC, the machine allows for multiple stages of pressurization. It can give first pressurization, exhaust according to the preset exhaust number and exhaust time, and then pressurize the material for many times automatically. When the pressurization time is reached, the system automatically depressurizes, the oil from the hydraulic pump is drained, and all movable platforms and attached plates will be lowered to their original positions with the help of the equipment’s own weight.
For vulcanizing fine rubber products with complex shapes, we recommend using a vacuum vulcanizer.
When the plate vulcanizer is working, the most power-consuming parts is the heating tubes inside the two heating platens. When the machine is started, especially during the platen heating stage, a large current input needs to be maintained, and the entire machine will be maintained in a high power state. The main function of the ammeter is to monitor the current changes of the heating devices to determine the operating status of the equipment, including whether the current exceeds the standard and whether the equipment is operating normally. This is crucial to ensure the stability of production and the long-term operation of equipment.
The rubber vulcanization process is a process that is processed at high temperatures. From low temperature to high temperature, it possible that the material volatilizes, the rubber material is not dense, there are gaps, excess rubber material is extruded and discharged, and vulcanization gas is released. Let’s imagine that the mold cavity is filled with air before filling the raw material. When the mold is pressurized, the raw material flows into the mold cavity. Because we set a lower pressure value for the exhaust, the lower pressure cannot allow the raw material to fill the mold cavity before exhaust, leaving a space for air. The air in the mold cavity is squeezed into the depth of the mold cavity as the raw material is filled, and is compressed to generate a higher air pressure. At this time, if we exhaust the air again, the air inside will be easily discharged out of the mold cavity due to the higher air pressure.
Sometimes the fluidity of the raw materials is not ideal, or when the secondary feeding method is used, if the pressure is in place at one time, it is easy for the raw materials to fail to completely fill the mold cavity, causing the product to be short of material, but with large burrs. Setting low pressure exhaust can solve this problem very well. The raw material will first flow into the entire mold through low pressure, and then fill all the mold cavities through high pressure.
Before vulcanization, various parameters of the vulcanizer need to be adjusted, among which the number of exhausts is a very critical one. The principles for adjusting the exhaust frequency of the vulcanizer include:
1)Appropriately change the number of exhausts according to the size of the stroke.
2)The specific number of exhausts should be determined according to the needs of the process and the actual situation, but it must be stable and consistent.
3)Avoid too much or too little exhaust to avoid affecting the vulcanization effect and vulcanization quality.
4)Clean the exhaust pipe in time to avoid blockage.
- Rubber materials contain moisture during mixing, storage, and use. The moisture is not removed, resulting in bubbles or moisture due to weather changes.
- The mixing operation is not standardized, resulting in uneven rubber mixing and incomplete and even dispersion of the compounding agents.
- The mold design is unreasonable. Improper setting or blockage of the vents will also produce air bubbles. When the raw materials are mixed, the air will be trapped inside the material, causing the material and air to enter the mold together during the processing. If the mold does not have the exhaust groove so that air can easily be trapped inside the mold, causing bubbles to form in the product.
- There is no exhaust process during the vulcanization process.
- Insufficient vulcanization and the immature rubber material appears to have bubbles.
- Insufficient vulcanization pressure.
- The vulcanizing agent contains many impurities. Small molecule impurities are decomposed in advance and bubbles remain in the product.
- The product is too thick. If there is too little rubber material, the rubber will transfer heat slowly. After the surface is vulcanized, the fluidity of the rubber will decrease, resulting in a shortage of material, so bubbles may occur.
- Formula problem, and the vulcanization system needs to be improved.
It is easy to understand that the upper layer of the flat plate vulcanizer is used for heating. The plastic polymer particles are heated and melted to form thin sheets under a certain pressure. So what is the purpose of using water cooling in the lower layer? After the sample is molded on the upper layer of the flat vulcanizer, some materials have a large shrinkage rate and cannot be opened immediately, but the process from the high temperature in closed mold state to room temperature is very slow. In order to speed up the production of test pieces and avoid large-area shrinkage of the material, we need to quickly transferred the mold from the upper layer to the lower layer, and the lower plate is supplied with circulating water to reach cooling purpose, which can greatly improve work efficiency.
This type of flat vulcanizer is generally used to process plastic materials, composite materials, polymer particles and other materials. Cooling is one of the common processes for making test pieces before tensile testing, impact testing, light transmittance and other tests.
Vulcanization is a process that the semi-finished products made from appropriately processed rubber materials (raw rubber, plasticized rubber, mixed rubber) with certain plasticity and viscosity are transformed into soft rubber or hard tough rubber products under certain external conditions through the action of chemical factors or physical factors to obtain desired performance. During the vulcanization process, external conditions such as heating or radiation cause a chemical reaction between the raw rubber and the vulcanizing agent or the raw rubber and the raw rubber in the rubber component, and the linear rubber macromolecules are cross-linked into a three-dimensional network structure. Through this reaction, various properties of rubber are greatly improved, allowing rubber products to obtain physical, mechanical and other properties that can meet the needs of product use.
Under a certain temperature and molding pressure, in order to change the rubber material from plasticity to elasticity and maximize the cross-linking density, the time it takes to optimize the physical and mechanical properties is called the rubber product vulcanization time. Usually it does not include auxiliary time for the operation process.
Vulcanization time is closely related to vulcanization temperature. During the vulcanization process, when the physical and mechanical properties of the vulcanized rubber reach or approach the optimal point, this degree of vulcanization is called optimum vulcanization. The vulcanization time required to achieve optimum vulcanization at a certain temperature is called optimum vulcanization time. A certain vulcanization temperature corresponds to a certain optimum vulcanization time. When the rubber compound formula and vulcanization temperature are constant, the vulcanization time determines the degree of vulcanization. Rubber products of different sizes and wall thicknesses control the degree of vulcanization by controlling the vulcanization time. Generally, the larger the size or thickness of the product, the longer the vulcanization time required.
Rubber vulcanization temperature is one of the three major vulcanization factors. It is the basic condition for rubber vulcanization reaction (cross-linking reaction) and directly affects the rubber vulcanization speed and product quality. Like all chemical reactions, the vulcanization reaction accelerates as the temperature increases, and more low-sulfur cross-links are easily generated. when the vulcanization temperature is low, the speed is slow, the generation efficiency is low, and more polysulfide cross-links are generated. The vulcanization temperature generally applies to Van’t Hoff’s law, that is, for every 8~10°C increase in temperature, the reaction speed approximately doubles; or in other words, the reaction time is approximately reduced by half.
Vulcanization pressure refers to the pressure that the rubber compound bears per unit area during the vulcanization process. Generally speaking, except for some cloth and sponge rubber, other rubber products require a certain amount of pressure when vulcanized. Rubber vulcanization pressure is an important factor in ensuring the geometric dimensions, structural density, and physical mechanics of rubber parts. It can also ensure that the surface of the parts is smooth and defect-free, and meets the sealing requirements of rubber products.
When rubber products are vulcanized, pressure needs to be applied. The purpose is:
- Prevent bubbles from forming in the rubber material and improve the density of the rubber material.
- Make the rubber flow and fill the mold to produce products with clear patterns.
- Improve the adhesion between each layer in the product (rubberlayer and cloth layer or metal layer, cloth layer and cloth layer), and improve the physical properties of the vulcanized rubber (such as flex resistance).
Generally speaking, the selection of vulcanization pressure should be determined based on product type, formula, plasticity and other factors. In principle, the following rules should be followed: for greater plasticity, the pressure should be smaller; for thicker products, many layers, and complex structures, the pressure should be larger; for thin products, the pressure should be smaller, and even normal pressure can be used.
The pressure F required for vulcanizing rubber products depends on the pressure area “S” of the vulcanized product or mold and the required unit pressure “P”.
F=S*P
In the formula,
F – the pressure required for vulcanizing rubber products, in N
S – Pressure area of the product or mold, in m2
P – The unit pressure necessary for the vulcanized product required by the process, in Pa
1) The plastic deformation of rubber is large before vulcanization. After external force is applied, the randomly curled rubber molecules are in a straightened state. If they are further stretched, slippage will occur between the molecules. After the external force is removed, the rubber returns to its original state, but molecular slippage cannot be restored, resulting in large permanent deformation of the rubber. After vulcanization, a network structure is formed between the rubber molecules and the permanent deformation is small.
2) Rubber is easy to dissolve before vulcanization. For example, natural rubber can be dissolved in gasoline, benzene, and toluene. Rubber swells after vulcanization. The size of swelling depends on the degree of vulcanization. The greater the cross-linking density, the smaller the degree of swelling.
3) The thermal stability of rubber is not good before vulcanization. It becomes sticky when exposed to heat and becomes hard when exposed to cold. After vulcanization, the heat resistance and cold resistance of rubber are greatly improved, and the stability against hot and cold is greatly improved.
4) The strength of rubber is low before vulcanization and becomes high after vulcanization. For example, the tensile strength of natural rubber NR is only 1.4-2.5 MPa, but after vulcanization processing, its tensile strength can reach 17-25MPa.
Get a Customized Quote for a Lab Hydraulic Press that Best Meets Your Needs
Tell us about your unique testing requirements to get a personalized solution from AmadeTech